The Rutan Boomerang
Meet the Boomerang: a one-of-a-kind experimental aircraft designed by Burt Rutan and maintained and operated by the Aerocrafted team.
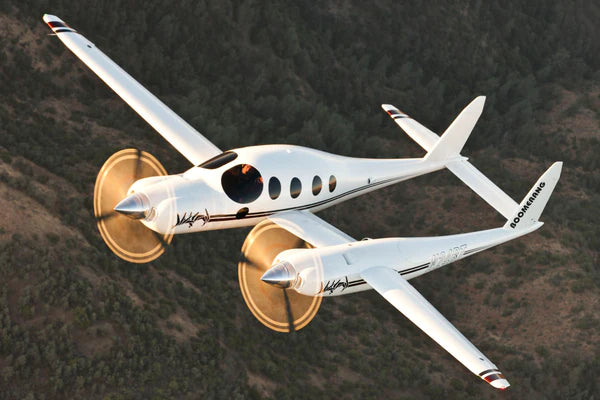
The number one question Aerocrafted gets asked when operating the Boomerang is, “Why does it look like that?” The Boomerang’s striking design is apparent from its first impression, but even more impressive is the engineering that fueled its appearance. The basic goal: create an aircraft that is both efficient and safe. The solution: placing the engines closer together than a normal twin engine, which results in a unique asymmetrical design.
Meet the Designer
Burt Rutan received his Bachelor of Science degree in Aeronautical Engineering from California Polytechnic State University San Luis Obispo in 1965. Fittingly, the Boomerang is still operated on the Central Coast of California by the San Luis Obispo based Aerocrafted team.

The 1970s and '80s were a prolific time in Burt’s career, as he created a handful of very unique, fast, and efficient homebuilt aircraft designs. He pioneered the simplified method of building curvy airplanes out of shaped foam and fiberglass (without the need for molds).
He founded Scaled Composites to help facilitate the aerodynamic engineering design of experimental aircraft for both corporate and military markets. Prior to this (during his Rutan Aircraft Factory days) Burt designed the Voyager: the first aircraft to fly completely around the world without stopping to refuel. This is just one of his many impressive accomplishments. You can view more of his work and story at www.burtrutan.com.
Burt’s work at Scaled Composites in the late '80s and early '90s kept him very busy, but he still found time to design and engineer the Boomerang, his passion project. Though his concept was initially met with skepticism from his peers, he was empowered to follow his design instincts, as the Boomerang was his own personal project and airplane. He wanted an airplane that was safe and efficient. He had previously achieved these goals separately in different aircraft: the Catbird was efficient and the Defiant safe. The Boomerang had to be both.
The Status Quo: Traditional Twin-Engine Aircraft vs Centerline Design
In order to understand why the Boomerang is so different, it helps to take a step back and understand what the status quo for aircraft design was at the time. Since the 1930s, the common design for a twin-engine aircraft remained mostly constant: an engine mounted on each wing, with an airframe that’s the same shape on either side of the centerline. The main benefit of twin engines is safety in redundancy of systems. If one engine malfunctions, the other keeps the aircraft flying. This is understandably important when considering what engine failure on a single engine aircraft would look like over large bodies of water or at night.
However, the basic twin engine design has its flaws. When a traditional twin-engine aircraft experiences one engine failure, it’s not only going to struggle with the reduction in power, but also with the asymmetrical thrust. The further away the engines are from the centerline of the aircraft, the more dramatically the problem of asymmetrical thrust will present itself.
Some aircraft designers have addressed the asymmetrical thrust and critical engine issues with a ‘centerline thrust’ solution. One engine is mounted in the front and one in the rear, resulting in a push-pull configuration. This does put all of the thrust where you’d ideally want it, but also comes with drawbacks; the cabin becomes quite noisy, and will have significantly more vibration than a traditional twin engine.
The Cessna Skymaster is an example of a push-pull aircraft, but it lacks efficient performance due to several design flaws. The Skymaster cabin became known for being loud and full of vibration. The aircraft also didn’t have adequate room for baggage, as the logical location for storage was taken up by the second engine. While the Skymaster solved certain safety problems with its centerline design, it compromised in the areas of utility and performance.
In an effort to correct some of these common design hurdles, Burt Rutan created the Defiant in the late 1970s. As a push-pull aircraft, the Defiant utilized a canard layout that was eventually made available as a homebuilt aircraft. Like the Skymaster, it succeeded in offering increased safety in the event of an engine failure, but ultimately lacked efficiency.
Basic Boomerang Design Concept
Burt’s basic Boomerang design requirements started with these parameters: more interior room than the Long-EZ, space for five, great speed and efficiency (like the Catbird), and two engines for enhanced night and over-water flight safety (like the Defiant). Additionally, he wanted to retain the good handling qualities that his centerline thrust Defiant possessed, without the other drawbacks that came with existing push-pull designs.

Beginning from a blank slate, he brainstormed unique ways to reduce how far off the centerline engines were typically mounted. He accomplished this by moving the right engine to the fuselage, resulting in both engines being closer to the center of gravity. This creates a reduction in drag, due to having less frontal area than a traditional twin engine (with two engine nacelles and a fuselage). He then modified the rest of the airframe to further reduce the negative effects experienced during an engine failure, regardless of which engine failed. He implemented a number of ‘odd’ changes required to allow the airplane to remain in proper balance with various compositions of fuel, passengers, and cargo loads.
The Boomerang’s Design Details
Burt’s work at Scaled Composites put him on the leading edge of the transition to using carbon fiber for strong and lightweight structures. The Boomerang took full advantage of this technology, but because of the significant resulting reduction in weight, it actually made the balancing of engines, fuel, and people more difficult. In order to mitigate this Burt designed the wings to sweep forward, giving the Boomerang its striking appearance. The forward swept wings are primarily used to move the aerodynamic center of the aircraft further in front, to compensate for the weight of the engine being placed on the nose of the aircraft. The inherent strength of the carbon fiber made the aeroelasticity concerns of the unusual forward swept design manageable—something not previously possible with more traditional materials.
The empty weight of the Boomerang is 1,367 pounds lighter than a pressurized Baron, which is an astonishing weight savings. Some of this is attributed to the use of smaller 4-cylinder engines. However, the reason these smaller engines can be utilized in the first place is because the overall airframe is significantly lighter.
The carbon fiber structure also allows the Boomerang to have its cabin pressurized to 4.6 psi. Conversely the Baron is only able to be pressurized to 3.8 psi. This is significant because at 25,000 feet the Baron cabin has the feel of 12,300 feet elevation. In comparison, at the same altitude, the Boomerang has a cabin feel of 10,150 feet. And while the Baron can be configured with a total of six seats, cargo space is relatively limited. The Boomerang, with its respective five seats, retains the left side boom baggage space. This means that longer items can be ‘checked’ easily while never compromising passenger comfort.
The Boomerang uses two Lycoming 4-cylinder turbocharged engines (TIO-360). However, they have different dash numbers, with one rated at 210hp, and the other at 200hp. While this may seem like a highly intentional design choice, it really came down to Burt’s interest in keeping costs down. At the time of design, he simply had these two engines available and within easy reach, which is how they wound up on the airplane. In fact, to further save money, the Boomerang was built after hours by Burt and a handful of other Scaled employees, who volunteered their time to help make his design a reality. Even though this airplane is cutting-edge and full of advanced engineering ideas, it is also very grassroots. That’s always been Burt’s way.
The Boomerang is able to fly on either single engine—at full power with no rudder input—while retaining the ability to stall. Due to the forward swept wings, the wing roots stall long before the wing tips. This means the pilot retains full roll control of the airplane while it naturally drops its nose, increases airspeed, and begins flying again. If the pilot holds the nose up, the airplane will continue to stall and recover, while retaining directional control. In contrast, when flying a traditional twin engine aircraft on one engine in an emergency scenario—even at full rudder deflection—the pilot cannot prevent the airplane from turning into the failed engine. This leads to a total lack of control of the aircraft prior to it stalling. Additionally, the Boomerang has a tail behind each engine. This was designed so there is always an engine blowing air over one of the tails, which increases rudder and yaw effectiveness when flying at low speeds.
The Boomerang has two doors for entry: a small airstair on the right behind the wing (for the three rear passengers), as well as an unusual windshield door on the right (for the two seats up front). Being pressurized, the windshield door opens inward and then slides aft. There’s also a pop out step when the windshield is opened, to help with entry and exit. This door configuration allows the wing spar to be continuous, improving strength and reducing weight.
The fuselage structure utilizes a manual filament-winding system to create diagonal longerons, strategically positioned for load distribution and to define structure for the door and window openings. The wing spar is continuous, for added strength and to keep supporting weight down. It runs through the fuselage just behind the two front seats. Since it’s passing through at an angle, due to the unique wing shape, it makes even more sense that Burt staggered the front seats. The pilot sits on the right, in the forward most seat, and the second seat is a few inches aft, which shifts the interaction of their shoulders and elbows. As opposed to traditional side-by-side seating, the three additional seats are located behind the wing spar: all positioned more organically so that each person has their own space.
Both front seats have a side-stick controller, but only the right seat has rudder pedals. These pedals are unique, being both split, with a right and left side. Each side operates independent brake systems. The Boomerang does not have nose wheel steering, and instead utilizes differential braking. Each main gear leg has two wheels, which allows each wheel to be connected to separate brake systems via the split rudder pedals. This offers redundancy for both braking and steering.
The landing gear is quite unusual, with the nose wheel mounted on the left side of the fuselage, placing it a little more evenly between the two main gear legs. When retracted, it allows the wheel to sit just forward of the feet of the person in the left seat.
The main gear legs are positioned with the one on the fuselage sitting farther aft than that of the one on the boom. This ensures that the airplane doesn’t fall back on its tail when passengers climb in the rear door before anyone is sitting up front. That gear leg retracts forward, while the main leg on the boom retracts aft. Even though weight distribution on the mains is uneven, and they are not the same distance behind the nose wheel, the airplane behaves just fine during takeoff and landing.
Where the Boomerang really impresses, however, is in the air, with either both engines running—or just one. The wing loading is high, at about 41 pounds per sq. ft., which gives the aircraft a rock-solid feel. This also contributes to the high max cruise speed of 264 knots (304 mph). The wing is designed with the ailerons running essentially full span, but they also function as flaperons. Additionally, for camber control, the ailerons can travel upward, giving increased efficiency at high speeds.

Just as Burt had intended, the Boomerang is minimally affected by asymmetrical thrust in the event of an engine failure. This is primarily attributed to how close both engines are to each other. Viewed from the front, the gap between the prop discs is less than one foot. By comparison, on the Baron the gap is nearly six feet. The other measures that Burt put in place are less obvious. One such example is the placement of the left engine further from the effective centerline, so that in high angle of attack situations, when P Factor comes into play, the two thrust lines are very similar. There are also twin tails that ride in the prop blast of the engines, ensuring great yaw control.
Burt’s Favorite Creation
What seems at first glance like the craziest aircraft design ever seen, is actually the one Burt Rutan believes is his greatest achievement in General Aviation. The Boomerang offers extreme efficiency and utility, while also effectively eliminating the dangers of asymmetrical thrust in a twin-engine aircraft. It’s even more impressive when you realize this aircraft was designed without any wind tunnel testing or advanced computer design. Burt’s success in achieving his design goals is a tremendous accomplishment, and the Boomerang remains a shining example of the true spirit of experimental aircraft.
Aerocrafted is honored to keep the Boomerang’s legacy alive by operating it on the Central Coast of California, where Burt’s journey into aviation first began.

Performance and technical specifications of the Boomerang
Engines | Lycoming TIO-360A1B (200 hp) RHS Lycoming TIO-360C1A6D (210 hp) LHS |
Seating | 5 (includes pilot) |
Empty Weight | 2370 lb |
Max Fuel | 1026 lb |
Max Cabin Payload | 1000 lb |
Payload at Max Fuel | 865 lb |
Max Gross Weight | 4242 lb |
Wing Span | 36.7 ft |
Wing Area | 101.7 ft² |
Length | 30.6 ft |
Aspect Ratio | 13.2 |
Vmax | 283 knots true (326 mph) at 18,000 ft |
Max Cruise | At 22,000 ft and 75% power: 264 knots/304 mph at 1500 nm range |
Economy Cruise | At 24,000 ft and 50% power: 210 knots/242 mph at 2100 nm range (range includes takeoff, climb and 45 minute reserve) |
Max Climb | 1900 fpm (2900 fpm at 2800 lb) |
Stall Speed | 88 knots (at 4200 lb) or 73 knots (at 2800 lb) |
Pressurization | To 7000 ft at 22,000 ft altitude |
Gear Retract | Electric mains, manual nose |
Miscellaneous | Full-span aileron reflex |